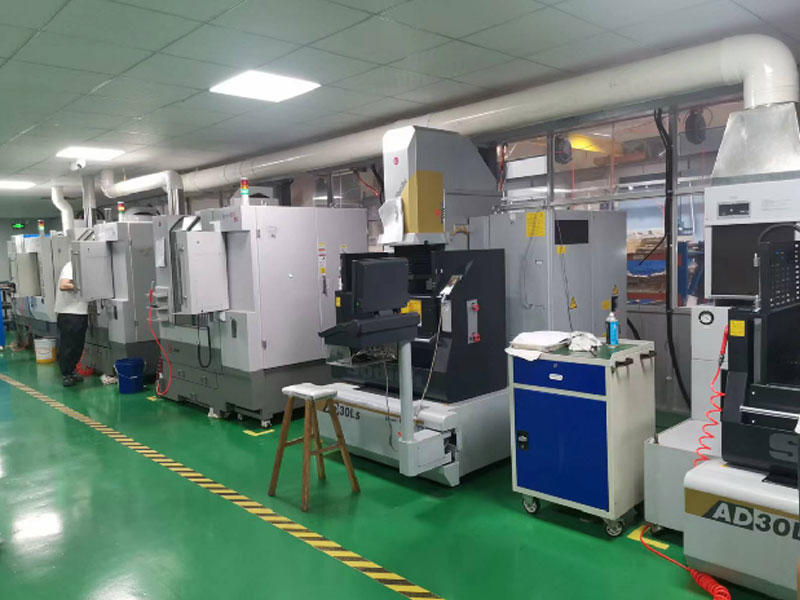
ABS 成型 批发商 出口商
ABS(丙烯腈丁二烯苯乙烯)成型是一种通用且广泛使用的制造工艺,可用于制造复杂且耐用的塑料零件。这种热塑性聚合物因其出色的机械性能(包括抗冲击性、耐化学性和易于加工)而受到各个行业的青睐。 ABS成型工艺涵盖多种技术,包括注塑、挤出和热成型,每种技术都有其独特的优点和应用。
注射成型也许是最常见的方法 ABS成型 。在此过程中,ABS 颗粒被加热直至熔化,然后在高压下注入模具型腔。该技术非常适合生产大量设计复杂的零件,例如汽车零部件、消费电子产品和家用电器。注塑成型的精度使制造商能够实现严格的公差和复杂的几何形状,使其成为许多应用的流行选择。注塑成型中的 ABS 成型工艺非常高效,因为它可以最大限度地减少浪费,并且可以快速生产零件,从而对于大批量生产来说具有成本效益。
挤出是 ABS 成型的另一种重要方法。在此过程中,ABS 被加热并被迫通过模具形成连续的形状,例如片材、管材或型材。然后可以将挤出的 ABS 切割成一定长度或进一步加工成成品。该技术对于需要长而均匀形状的应用特别有用,例如管道、面板和各种建筑材料。挤出的灵活性允许加入添加剂和填料,从而增强产品的性能。 ABS 挤出成型工艺的特点是能够生产大量且质量稳定的材料。
热成型是 ABS 成型的第三种方法,该方法包括加热 ABS 片材直至其变得柔韧,然后在模具上成型。该技术通常用于制造较大的零件,例如汽车内饰、包装和电器外壳。热成型工艺可分为真空成型和压力成型,每种成型工艺在最终产品中提供不同程度的细节和复杂性。真空成型更简单且更具成本效益,而压力成型可实现更复杂的设计。热成型中的 ABS 成型工艺有利于中低产量,因为与注塑成型相比,它需要的模具投资更少。
每一种 ABS 成型技术都有其特定的考虑因素和要求。例如,在注塑成型中,控制温度和压力对于避免翘曲或不完全填充等缺陷至关重要。在挤出过程中,保持一致的温度和流量可确保挤出产品的均匀性。热成型需要仔细控制温度,以实现 ABS 片材的适当柔韧性,确保其与模具良好贴合,而不会撕裂或产生薄弱点。
ABS 成型方法的选择通常取决于产品所需的特性、产量和成本考虑。对于复杂几何形状的大批量生产,注塑成型通常是更好的选择。对于更简单、更长的零件,挤压可能更合适。热成型非常适合细节不太重要的大型零件,并且可以接受较低的产量。
ABS 成型是现代制造中的关键工艺,提供了一系列满足各种应用和行业的技术。 ABS 的多功能性与这些成型方法的效率相结合,使其成为生产耐用和高质量塑料零件的流行选择。随着技术的进步,ABS 成型工艺不断发展,从而在塑料部件的生产中实现更大的创新和效率。无论是通过注射、挤出还是热成型,ABS 成型仍然是塑料行业的基石,推动着产品的创造,改善我们的日常生活。