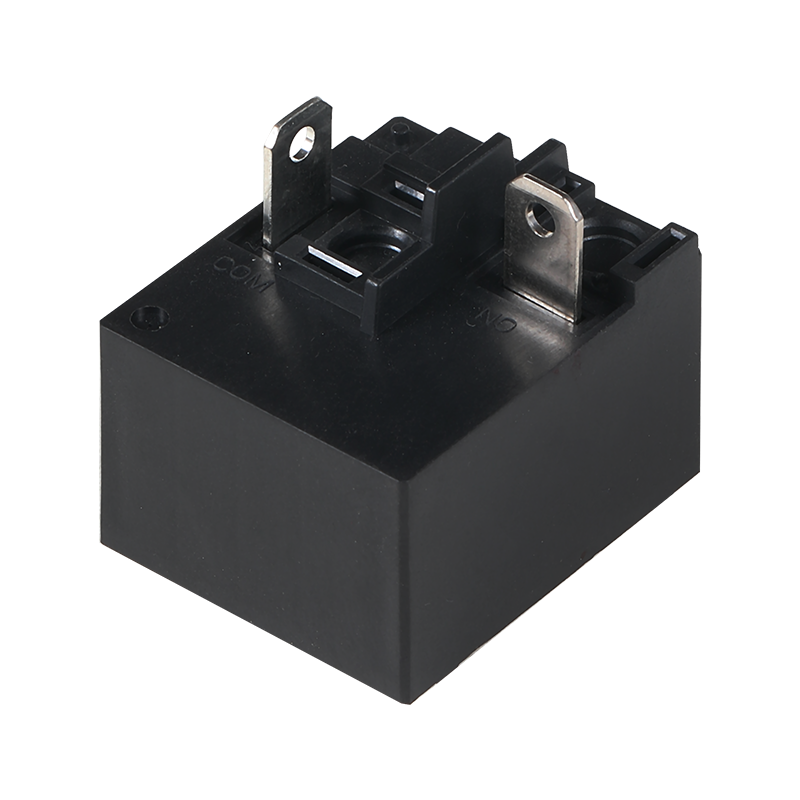
注射成型是一种制造工艺,已成为生产过程中不可或缺的一部分 各种塑料零部件 。它是一种大批量、高效的方法,广泛应用于汽车、消费品、电子和医疗设备等行业。
注塑成型过程涉及使用机器加热并熔化塑料材料,然后将其注入模具型腔。模具旨在创造最终产品所需的形状和特征。一旦塑料冷却并硬化,模具就会打开,成品部件就会被弹出。大规模注塑是指在短时间内生产大量相同的零件,这是通过过程的自动化和高效性实现的。
注塑成型的设置成本可能很高,但随着大批量生产,单位成本显着降低,使其成为大规模生产的经济选择。
注塑机可以生产具有高尺寸精度和一致性的零件,这对于需要装配在一起或满足严格规格的零件至关重要。
注射成型可使用多种热塑性材料,从而可以生产具有不同性能(例如强度、柔韧性和耐热性)的零件。
具有复杂几何形状(包括底切和复杂细节)的零件可以相对轻松地生产,而其他制造方法并不总是能够做到这一点。
该过程可以高度自动化,降低劳动力成本并提高生产速度。
注塑机和模具的成本可能很高,这可能对小企业或初创公司来说是一个障碍。
模具需要定期维护,并且维修或更换成本高昂,尤其是对于大规模生产而言。
虽然该工艺非常高效,但仍然可能存在来自浇口和流道的废物,它们是注塑工艺的一部分,不会成为最终产品的一部分。
该过程需要大量能量来加热和冷却材料,这可能是具有环保意识的制造商所关心的问题。
虽然注射成型可以生产复杂的零件,但仍然必须考虑一些设计限制,例如需要拔模角度以及无法在没有支撑的情况下生产具有悬垂特征的零件。
人们越来越关注减少注塑成型中的浪费和能源消耗。这包括使用回收材料、节能机器以及减少材料浪费的工艺。
可生物降解塑料等新材料的开发正在扩大注塑成型在优先考虑可持续发展的行业中的可能性。
机器人技术和先进自动化的集成预计将进一步提高注塑工艺的效率和精度。
数字技术的使用,例如用于模具制造的 3D 打印和用于流程优化的模拟软件,正变得越来越普遍。
虽然大规模注塑传统上与大规模生产相关,但大规模定制的趋势日益增长,即进行微小的变化以满足个别客户的需求。
综上所述, 大型注塑 是一种强大的制造技术,可为大批量生产带来显着优势。尽管面临挑战,大规模注塑成型的未来看起来还是充满希望的,创新将塑造我们未来几年生产塑料零件的方式。