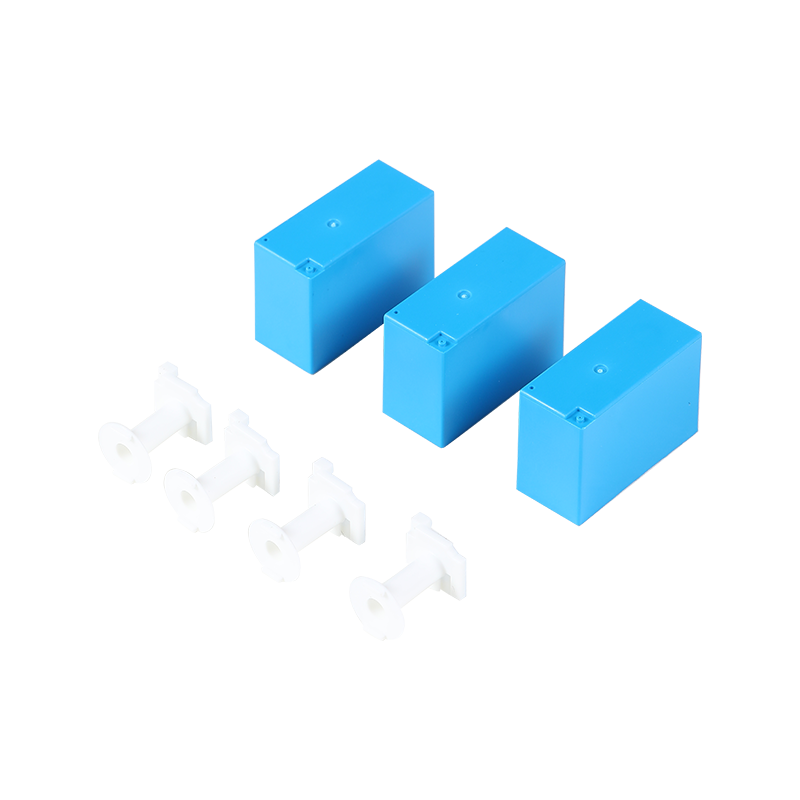
汽车行业长期以来一直处于创新的前沿,不断寻求提高效率、性能和安全性的方法。其中一项创新是使用 塑料注射成型 用于生产汽车零部件。这一工艺彻底改变了汽车的制造方式,带来了从成本效益到减轻重量等一系列好处。
塑料注射成型是一种涉及使用模具来成型塑料材料的制造技术。该过程首先将塑料材料(通常为颗粒形式)送入料斗。然后将其在桶中加热并熔化,在桶中混合并压入模具型腔。一旦模具被填充,材料就会冷却并硬化,形成型腔的形状。然后打开模具,弹出成品部件。该工艺高度自动化,可以大批量、高精度生产零件。
汽车零件模具设计用于生产各种组件,从小型内部配件到复杂的外部零件。通过塑料注射成型生产的一些更常见的汽车零件包括:
1. 仪表板:这些是大型、复杂的零件,需要精确成型以确保良好的配合和光洁度。
2. 保险杠:模制而成,用于在碰撞时吸收冲击力并保护车辆,通常由多种材料制成,以提高强度和灵活性。
3. 灯罩:这些灯罩可保护车辆的照明系统,并可承受高温和天气条件。
4. 内饰:门板、中控台和仪表板等部件通常由模压塑料制成,以获得一致且美观的饰面。
5. 外部部件:格栅、扰流板和车身面板等部件可以通过模压实现光滑、无缝的外观。
在汽车行业中使用塑料注射成型具有以下几个优点:
1.成本效益:该工艺效率高,与传统制造方法相比,可以以更低的成本生产大量零件。
2. 重量轻:塑料部件比金属部件轻,这有助于提高燃油效率并减少排放。
3. 设计灵活性:注塑成型可以创建其他材料无法实现的复杂形状和设计。
4.耐用性:汽车零部件中使用的ABS和其他塑料耐腐蚀,可以承受恶劣的天气条件。
5. 可回收性:汽车零部件中使用的许多塑料都可以回收利用,有助于实现更可持续的制造过程。
虽然塑料注射成型具有许多优点,但也存在需要考虑的挑战。模具制造的初始成本可能很高,并且该过程需要仔细选择材料以确保零件满足必要的强度和耐用性标准。此外,必须负责任地管理塑料生产和处置对环境的影响。
塑料注射成型已成为汽车行业不可或缺的一部分,为生产各种汽车零部件提供了一种经济高效的方法。随着技术的不断进步,能力 塑料注射成型 可能会扩大,进一步增强其在汽车零部件制造中的作用。注重创新和可持续发展,汽车行业塑料注塑成型的未来前景广阔。